Building a hardtop - the idea, concept and material choices (part 1)
- Sailing The Dream
- Feb 4, 2022
- 5 min read
Updated: Oct 24, 2022
Our Bimini project has been on the cards for a while.
When we first bought The Dream, we had tattered canvas work that desperately needed replacing. After the end of our first season, we got the opportunity to do it. An expensive project with a limited lifespan considering fabric only lasts a few years.
After living on board for four years, we became more and more convinced that a rigid Bimini was one of the items that would improve our life onboard considerably.
A rigid Bimini would give us better sun and heat (temperature irradiation) protection during the harsh summers and provide a solid roof for the winter, keeping the cockpit with a much nicer temperature.
I guess, if you are a purist sailor, the idea of a Bimini and Sprayhood ruins the sailing experience. We found that we prefer protection from the scorching sun during sailing and rarely dropped the Sprayhood and folded back the Bimini.

During the winter of 2019/2020, while in Greece and during the Covid19 lockdown, we decided it was time to design and put a plan in motion that would make the idea into reality.
With a sandwich construction system in mind, we inquired about materials and tried to find a suitable place to work. After a lot of hunting around and disappointment with the local chandleries, we found a local online supplier for the core material (XPS foam) we wanted to use and a Greek fibreglass supplier (Fibermax) that had the materials we needed with great quality and price.
The arrival of the XPS foam kept us entertained during the remaining months we stayed in Greece (still during the lockdown), allowing us to work on shaping all the pieces we needed for our design.
With our departure to Turkey in late March, the project was on hold until the end of the 2021 summer. The high temperatures registered in the south of Turkey during that period made it extremely difficult to proceed with our project. Given we had requested temporary residency in Turkey, it was just a matter of waiting for the end of summer to set the project back into motion.
Our biggest concern was the structural integrity of the new Bimini.
The ultimate goal was to install our rigid solar panels directly on it (3x22kg), avoiding a solar arch altogether.
To achieve this few strategies were taken into consideration in the design stage.
The new Bimini design was to follow the shape of the existing one. This curvature, although quite subtle, given its span (3800mm), ensures that the middle section of the structure won't sag under its weight.
We added a few extra details like an edge lip (around 100mm height) all around, which should help keep the overall shape by bracing the panels that form the new Bimini, preventing them from sagging in the middle by constricting them in position. This new edge lip also allows installing the shade curtains more neatly, hiding them when rolled up.
On top of these two strategies, we decided to incorporate some beams on the design to reinforce the entire structure in critical areas.
The beams would be built after fibreglassing the overall area and would also be made out of XPS foam and fibreglass. Making a double sandwich construction on these areas and should make them even stronger.
We aligned the position of the beams with the fibreglass cloth overlaps both on the underside and topside of the structure in an attempt to keep the remaining area of the Bimini panels as smooth and lightweight as possible while further reinforcing the beams areas.
At the same time, the construction of the beams would allow us to make allowances for embedded 12v wiring for lighting and other equipment to be installed on the top side of the Bimini, together with the solar panels.
This strategy allowed us to have overall only one layer of biaxial, twill and veil on each side. On the longitudinal beams, we have a total of five layers of biaxial, three layers of twill and three layers of the veil. On the transversal beams, we have three layers of biaxial, four layers of twill and three layers of the veil.
For the core of the new Bimini, we chose to use a 25mm thick XPS (Extruded Polystyrene) foam board due to its strength, yet lightweight and flexible characteristics, as well as for its insulating capabilities while being resistant to water absorption.
Easy to find at general construction suppliers at a good price, but most importantly, extremely easy to work.
For the fibreglass cloths, we decided to use the following types: 310gsm Biaxial, 270gsm Twill and 38gsm Veil.
We chose the 310gsm Biaxial cloth in a 45-degrees angle (to the roll width) variety instead of the normal 90-degrees. Our goal was to combat potential torsion of the entire structure caused by the boat movement.
The twill was chosen for its conforming characteristics, allowing us to ensure that all our curved areas would be treated more neatly and avoiding the usage of too much thickened epoxy in localised areas without the benefit or intent of added rigidity.
The idea behind the usage of the veil type cloth is not related to its structural capabilities (given its weight, there is not much structural value on its use) but with the desire of achieving a filled flat finish and minimising the fairing process. At the same time, it should give a bit more protection to high impact objects like hail by allowing a bit more resin coverage.
The combined cloths would allow us to achieve in the general area of the Bimini nearly 600gsm of fibreglass per side.
We decided to work with epoxy instead of polyester as it is inherently stronger and because of its reduced odour and toxic fumes while working. It meant, however, that we had to be more accurate with work times.
Building a rigid Bimini would also mean we would need to replace the entire existing Bimini structure with a more sturdy structural pole frame bolted to the deck and cabin top with backing plates and sub-deck support.
Our design would be a simpler but permanent structure, where the vertical poles would sit closer to the centre of the boat and not at the edge of the cockpit. Allowing a clear area on the side decks for passing but also allowing for extra holding places to grab on while circulating in our very wide aft cockpit.
We settled for stainless steel tubing with 35-38mm diameter and 3mm walls at six points with opposing angles and alignments. Ensuring the entire structure would be counterbalanced.
At structural support points, we planned plywood bearing blocks together with a large 200mm square by 8mm thickness aluminium fixing plate, laminated into the beams and the core with thickened epoxy. Giving a structurally sound place for the stainless steel support poles to be bolted.
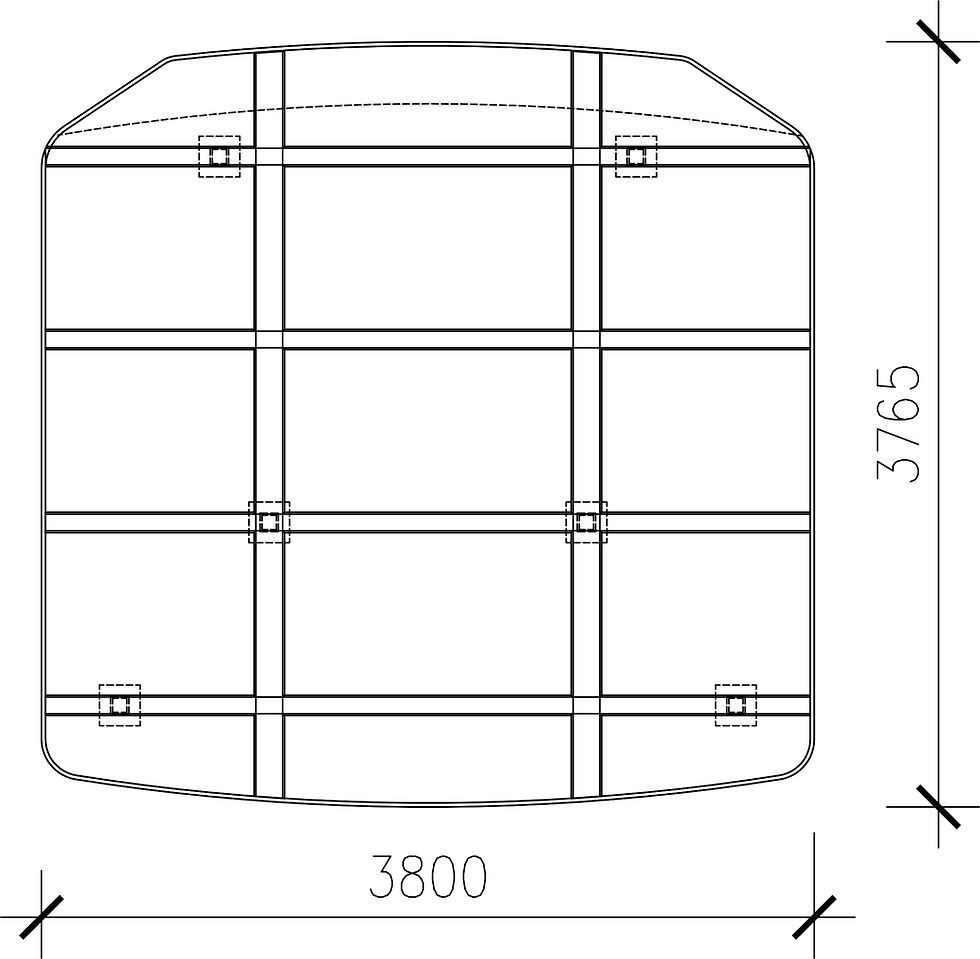
With all these details decided, materials purchased and with a good chunk of the preliminary work done while we were in Greece during the winter lockdown, it was time to get to work now that the summer season was coming to an end.
The only problem was that we were struggling to find a workplace close enough to an anchorage and that would not have people walking through or messing up with our stuff. Eventually, we were starting to become fed up with the situation and, in a moment of insanity, we wondered: Why the heck do we have a 50 footer?
And a decision was made.
We would build a good portion of the Bimini while at anchor on the foredeck!
***You can find other posts of this series at Building a hardtop - the construction (part 2) , Building a hardtop - Fairing (part 3) , Building a hardtop - joining the pieces and painting (part 4) , Building a hardtop - stainless steel works and installation of equipment (part 5) or Building a hardtop - costs, other numbers and conclusions (part 6)
***In the spirit of sharing our dreams and experiences we have shared this blog post in the NOFOREIGNLAND.COM website sailors community.
Comments