Coppercoat antifoul treatment - preparation & application (part 2)
- Sailing The Dream
- Nov 6, 2022
- 20 min read
With our return to Portugal and The Dream back in the yard as originally planned a few years back, it was time to tackle the much-wanted upgrade of our antifoul treatment to Coppercoat.
The Coppercoat kits had been ordered while we were still en route from Turkey to Portugal and were already waiting for us. It was now time to roll our sleeves and get to work.
The work in hand could easily be divided into two phases, preparation and application.
Preparation was not only the most time and energy consuming but also the most important. Coppercoat requires meticulous preparation.
The first step was removing old antifoul. Because The Dream had only had antifoul applied three maybe four times sanding was the best option, scraping or even sandblasting would potentially create more work due to its more destructive nature although giving first signs of results faster. There was also the issue of not knowing if the hull had been treated by the factory with a barrier coat, those two options would have easily damaged the treatment if it had been done.
Sanding the hull was a backbreaking job. The awkward work position, the weight of the sander machine, and the created dust all contributed to the challenge. Even the protection gear was an issue due to the summer temperatures, making us sweat profusely under the jumpsuit and the protective goggles that constantly fogged up.
Within the first few days of sanding we had gained a good understanding of how toxic antifoul paint is and how dangerous to one’s health the entire process of stripping it can be if not correctly protected.
The one thing we would have done differently would be to buy full face masks, but we already had the protective goggles and respirator masks from the hardtop construction project, and we did not want to spend another 200€ each for another mask.
The very small areas of exposed skin, maybe the equivalent of 15mm wide by 30mm long on each side of the face were feeling and looking burnt after only a short while. We immediately tried the trick used when working with fibreglass by applying baby talcum powder to the exposed skin. The first attempt did not turn out as well as we hoped for with the talcum powder mixing up with the antifoul dust. On a second attempt, we applied a thick layer of pawpaw cream followed by the talcum powder creating the protective barrier we needed on that sliver of exposed skin.

We worked hard and avoided taking breaks often. It felt that restarting after each break was even harder, so we opted for just a quick stretching of our backs and arms muscles whenever we needed to change the sand discs.
The yard workers were initially quite puzzled to see owners doing their work but soon warmed up to us coming quite often to check on progress they shared some tips and congratulate us for our efforts. After all, we understand how hard this kind of work is. They were surprised with our techniques and results, I guess they thought with our experience level (the one they thought we had), the hull might turn out to be a huge mess, full of depressions. That was not the case, the hull was very smooth, and the final result was as good as theirs, if not better.
This stage of the preparation of the hull was not only backbreaking but also psychologically challenging. In the beginning, the progress seems to be none, you sand, and you sand, and nothing the hull is as black as it was, to begin with, although by now you are covered in black also.
We started using 120-grit paper, and within an hour we gave up on that and switched to 80-grit for one attempt before deciding we needed to first blast the top layers of the antifoul paint with 40-grit paper and then switch to the 80-grit.
It was amazing the amount of dust the 40-grit paper released the moment the black in front of us started changing to a more brownish tone (much older antifoul) or a grey it was time to change to the 80-grit paper. The sanding of the oldest layers of antifoul and the antifoul primer was the most difficult part and most time-consuming, under it a white silvery layer became exposed. In some areas where we went a bit deeper a green layer showed up leaving us puzzled, we had no idea why were we seeing green.
We contacted Coppercoat by email and sent some photos. They commented it could be a barrier coat product (probably Gelshield because of the green colour) and that if we were not sure we could perform an easy test and confirm if it was a two-part epoxy product. That was crucial to be determined as it would dictate if we needed to sand deeper until we reached the gel coat or if we could work only up to this layer. The test was to simply wipe an area with Acetone and a clean towel, if it came clean it was a two-part epoxy, if it left traces of product we would have to keep sanding.
We performed the test a couple of times and even made a little clip to send back to the Coppercoat team, we were all in agreement it was a two-part epoxy product.
This was good news, it meant The Dream hull had been treated with a barrier coat from the factory, and that meant the hull was well protected from water ingress.
The guys at the yard had already commented on how dry our hull looked and felt, given that we had commented that in 9 years (most time in the water), antifoul had only been applied three or four times.
Armed with this knowledge we powered through our task.
John developed a technique of first blasting the excess antifoul, then reticulating areas of the hull using the 40-grit paper and then switching to the 80-grit to finish removing the bulk of the antifoul paint. This made for a reasonable pace and progress.

Once we cleared the bulk of the antifoul, we did a light round of sanding with 120-grit paper to ensure we finished the sanding with a smooth result.
Every few days during the sanding process we would pressure wash the hull to help remove the dust released and keep the sanded areas from accumulating contaminants that could be absorbed by the newly exposed product.
It took us 16 days, and 145 man-hours to remove all antifoul paint (except the base of the keel bulb)!
At the same time, we were removing the old antifoul paint we took the opportunity to abrade the area we were going to raise the waterline with 120-grit paper.

Once all the sanding was done we washed the entire boat a couple of times to ensure all the dust was removed, and to assess the quality of our work and the general condition of the hull. We were quite pleased to find the hull was smooth and dry, with no signs of blisters or any other issues, there was just a few areas we found were not well covered with the barrier coat, but since we were going to raise the waterline and Coppercoat had advised us to apply a few more coats of barrier coat on the keel (although it had already been treated with barrier coat from factory) before applying the Coppercoat we figured we could address those areas too.
At this point we had a big hiccup on our project, the yard workers informed us they would need to relocate The Dream to another place within the yard due to the music festival happening just across the street.
After an initial shock, we discussed with the travel lift operator where he would install the hardstand posts after moving us to the new spot.
We decided to take advantage of this situation and see it as an opportunity to test the Coppercoat application in small areas. This way we could apply Coppercoat in the reverse of how it’s usually done, starting with the chock areas first (where the handstands support the hull) and then the remaining hull.
With the areas defined we quickly prepared them to be worked on the next day. The following morning quite early we had our first experience applying the Coppercoat, and what a great experience it was.
We divided one kit in half, each kit allows an area of 4sqm to be fully treated and we calculated the total areas defined for the new handstands locations to be shy of 2sqm. With the help of a precision scale and syringes, we then divided the half kit into five batches to be mixed.
Getting the right timing to start mixing a new batch was a bit challenging, the first applied coat is the one that not only takes more time it also takes more product. Preparing the actual batch is quite straightforward but mixing it properly does require time. First, you need to ensure parts A and B are well mixed and then add the copper powder slowly while mixing at the same time, the entire concoction becomes heavy and thick, ensuring the copper did not accumulate in the corners of the mixing pot is the challenge. By now the colour is a bit like a light-coloured chocolate mousse.
Once it’s all well mixed you add the right ratio of Isopropyl Alcohol and mix again, the trouble is by now you are used to a thick and heavy mixture and with the Isopropyl Alcohol all of a sudden you can make a mess because it became less thick. At this point you notice the change of colour as the copper powder inevitably tries to go to the bottom of the mixing pot, a good mixing returns the concoction to its creamy state (not as thick as before) and original colour. I kept a close eye on this subtle change of colour both on the mixing pot (because you don’t pour the entire mix in the tray) and the tray giving it another stir and bringing any silted copper back in suspension on the mix. In the end, this ensured that very little copper was left to be applied (basically the wastage was just what stays in the roller).
If mixing has its challenges so does the application itself.
When we first rolled the Coppercoat onto the hull surface it seems to go very thinly almost like it doesn’t stick or cover much, but we found this first coat is just like a wetting out of the surface. We also found if you went back over the surface to try to get a better cover that it would just lift off the surface and make a mess. In the end, we found one pass in a consistently even layer was best, then leave it to tack off before the second coat and then repeat until five coats were achieved. For each coat, we found that the cover was increased and by the end of the fourth coat you had a complete cover and the fifth was like icing on the cake. Because we started with the patches we were able to work our way around the boat from patch to patch, by the time we had finished a round of the patches we were ready to start over with the next coat. This technique would help us understand how could we tackle the greater task of treating the remaining hull with just the two of us.
With the Coppercoat patches done we could proceed with our original work schedule.
It was quite a few fun days applying the Gelshield barrier coat scheme in alternate layers of green and grey, keeping in mind that the last coat should always be grey.
We gave four coats to the new waterline, bow tip, rudder and patches and we gave six coats to the keel and bulb. We gave the same treatment to all our Truedesign seacocks.
After a few days of curing, we gave a light sanding of these areas with 120-grit and we were relocated to our new spot in the yard. The travel lift guys were kind enough to leave us hanging on the travel lift slings overnight allowing us to work on the base of the keel bulb. Removing the remains antifoul, apply a primer and then the necessary barrier coat scheme as we had already done in the remaining keel.
After being lowered to the handstands we rushed to remove the antifoul patches where the handstands used to be in the old location.
With all the hull preparation done the focus now was making sure the entire boat was well washed with soap a couple of times to guarantee there weren’t any residues from the sanding job left, then we pressure washed the hull a few times to be sure there were no residues of soap and waited for the right weather conditions to apply the Coppercoat.
We used masking tape to create a "dew skirt" all around the boat just above the waterline that should protect the hull from any dew or condensation drip formed during the night.
Eventually, the right weather conditions presented themselves after a couple of days when we found the teak decks to be dry early morning.
We decided to start the application of Coppercoat on a Friday, it was a slow period at the yard with many of the workers on vacation and reduced staff during the weekend. This would reduce the chances of interruptions and problems with boats being washed or sanded nearby.
We arrived at the yard extremely early in the morning, confirmed that all was dried and proceeded immediately with wiping the entire hull with Isopropyl Alcohol twice. Then we prepared the mixing station and all the buckets, trays and rollers.
With our previous experience applying the Coppercoat and the warm temperatures, we decided that with just the two of us working our approach to the task could not be the one advised by Coppercoat, where you start on one side and just keep on painting and mixing until the entire side of the hull has the necessary coats. The warmer temperatures meant by the time we would finish the first coat on one of the sides the area where we had started would already be too dry.
We needed smaller working areas so the day before application we measured the hull and calculated strips of approximately 3.5sqm marking these with tape on the gel coat above the waterline, this would ensure we would have the correct timing for all needed coats and that the correct amount of copper would be applied throughout because we would prepare one kit (that is enough for 4sqm) and keep applying it on our defined 3.5sqm areas until we ran out the kit.
We had originally calculated that 16 kits would be needed but purchased 18 just in case, in the end, our math was right.
We took care of the hull for two consecutive days and tackled the rudder and keel on the third. By the following Monday, all that was left to do on this project was to paint the base of the keel bulb (the plan was to stay on the slings during the weekend before splashing) and give a light abrasion to the fully cured Coppercoat to activate it.
We allowed nearly a month of complete curing time (12 days of curing before activating the Coppercoat), after that we finally had The Dream lifted from the handstands to paint the base of the keel bulb. This time we would try and speed up some of the processes with the help of a heat gun. The travel lift, unfortunately, broke just two days before our scheduled lift date (a Friday) and only got repaired by Saturday after lunch, this allowed us only 42h curing time for that last patch.

Day 1 (2022-05-27)
John performed a test sanding in the rudder while I applied the masking tape to define the new raised waterline.
Day 2 (2022-05-28)
Short work day, but it was truly the day we started working on the hull.
This is the result of three hours of solid sanding with two sanders.
John started sanding the hull at the stern area due to the day breeze, using a compressed air orbital sander (150mm) and mostly 80 grit discs.
I started working on the keel using a 240v orbital sander (125mm) using 80 grit discs also.
It is safe to say John is a much better sander than me.
Day 3 (2022-05-29)
Six hours work day.
We tested a few different brands and another variety of 3M sanding discs, and eventually, we ran out of sanding discs.
Progress is slow due to the awkward working position and the sandpaper quality (tomorrow will order this new variety of 3M if they cannot order the one we prefer).

Day 4 (2022-05-30)
Another solid six hours workday.
Progress is slow still having some issues with the sandpaper quality for my sander.
John is developing a technique that allows him to achieve much better results. His progress for today is easy to identify from previous efforts, and in the same amount of work time, he managed a bigger area.
John has the power! And the pain, the muscles are complaining.
As for me, what can I say? Smaller sander, bad sandpaper and poor technique.
I manage to clear almost as much area on the keel as the previous day but without John's help. I worked a bit more on the starboard side of the keel but still not completed.
The day ended with another trip to the hardware centre to buy me a compressed air sander the same model as John's because at least we can find decent sandpaper for that one now.
If only we could be sponsored by 3M and Voltaren.
Less than 20 work hours of sanding old antifoul and this is how the 1st stage filters of our 3M masks look.
Besides these KN95 (particulate filter), our 3M masks have another set of filters to protect our lungs.
Imagine all the pollution we have been leaving in the water as these are self-ablative paints full of nasty chemicals.
Another reason for us to be moving to Coppercoat is to avoid contributing to sea pollution by using a more passive and efficient solution.

Day 5 (2022-05-31)
As per the advice of the Coppercoat team, we made a test with Acetone to determine if the products applied before the old antifoul primer are the two-part epoxy system Gelshield (the green colour suggests that it should be that product). And after testing it was indeed confirmed that these two products are a two-part epoxy product!
This means The Dream hull, rudder and keel were treated from the factory with a barrier coat product, and that is excellent news for us because it means the hull has been well protected from the sea and is dry.
It also means we do not need to sand the hull deeper until we reach the Gel coat (we only need to finish removing all the old antifoul and primer).
Day 6 (2022-06-02)
Today we did a six-hour workday because it started downpouring, and we had to stop standing. On the bright side, because there was quite a bit of wind, the rain washed away the dust from the hull, allowing a better view of the efforts.
John is still powering through the challenging working position with great results on the hull overall.
I started working on the original waterline, a much easier position to work in but requires an A ladder to reach the areas to be sanded.
There are good changes tomorrow we will finish the 40 and 80-grit sanding of the entire starboard side.
We have also been working on the bulb when the sanding discs are nearly finished (not good enough for the sander but still ok for the spot sanding) and when our arms and back need a break.
It’s progressing quite well.
Day 7 (2022-06-03)
Today was another workday ruled by the weather due to the several rain showers we suffered. It ended up being only a five-hour workday.
The progress is not easy to identify because the starboard side of the boat (first two photos) was the most affected area due to the wind that accompanied the rain showers making our work surfaces wet.
John managed to keep working on the underside for a long time until there were no more condition for him to keep working. I managed to keep working here and there at the bow and stern of the starboard side until it was no longer possible. Then I started working on the waterline on the port side because it was not affected by the rain (the boat itself was blocking the windy rain, so the waterline remained dry for quite a long time).
Both are now in a groove with the technique, and the results are pretty satisfactory.
There is nothing like having proper sandpaper!


Day 8 (2022-06-04)
The morning started with a heavy downpour, so we decided it was an opportunity to rinse the entire boat of the accumulated antifoul dust. Boatyards are such dirty places!
We also flushed the engine with fresh water thoroughly while we waited for everything to dry, and in no time we were back at sanding.
In the end, we only sanded for five hours instead of our usual schedule.
Starboard side bulk sanding is complete, and the port side is well advanced!
Day 9 (2022-06-05)
Short work day, just three hours due to weather conditions and a few other tasks that needed our attention.
Day 10 (2022-06-06)
We started the day hand sanding seacocks, we have between 15 to 20 of them.
Then when the chandlery opened we got more sandpaper discs and carried on with our Herculean task of sanding the hull out of antifoul paint.
In the end, we worked nearly eight hours, six hours bulk sanding!
Day 11 (2022-06-07)
The bulk sanding of the old antifoul is nearly finished!
Then we still have to go through all the spots that still need a bit more tough love to be sure we can advance to the next step
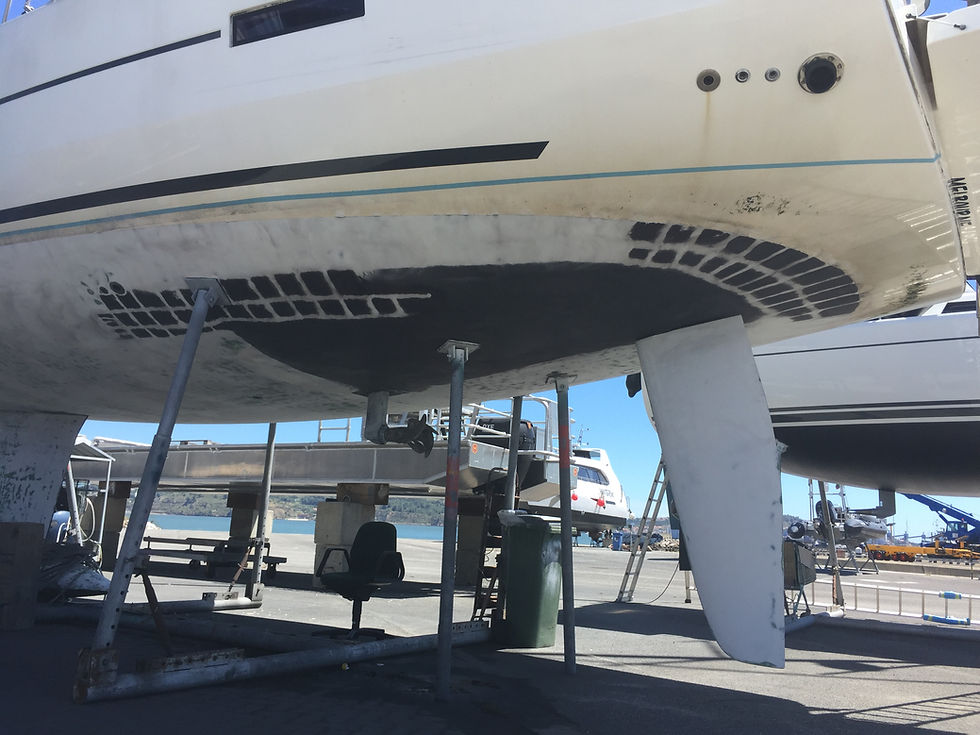
Day 12 (2022-06-08)
Short-day sanding. We took the opportunity to go over a few areas that required more attention.
Day 13 (2022-06-09)
The bulk sanding of the old antifoul is finally done!
As always, that last push is always the toughest, but then there is that moment you realise that it is done.
Day 14 (2022-06-11)
Today we worked for around four and a half hours.
John sanded the gel coat area with 120-grit paper to prepare for the application of a barrier coat before we can raise the waterline.
I think it is getting clearer how it will look.
I worked on the keel bulb, more precisely the underside of the bulb.
A difficult job given it requires to lay down on the floor to see what you are doing. Didn't manage to finish my task, but I’m very close to completion.
Applied protection paint on some spots that had little gel coat coverage and where the material used on the bulb construction became visible to avoid them rusting. This paint will be removed when I finish the task, and then we will care for it properly.
Day 15 (2022-06-16)
We took a break from work for a few days, didn’t expect the return to be this hard.
We washed the hull to remove any dust blown in while we were away.
John applied some epoxy filler on the bow to smooth some deeper scratches right on the tip of the bow caused by the occasional bang of the anchor.
Inspected our sanding work and gave a few more rounds of sanding here and there wherever we found still some traces of the old antifoul paint.
Day 16 (2022-06-17)
Sanded the epoxy filler we applied the day before and applied a bit more where we were still not happy with the smoothness of the surface. Protected that area with a plastic sheet to avoid getting wet while washing the hull.
We started preparing the hull to apply the barrier coat the following morning. Washed it thoroughly, then started cleaning the areas to be worked with Isopropyl Alcohol when one of the travel lift guys came to us and told us discreetly that we would have to be moved to another place. At the same time he was talking to us, three guys were marking some measurements on the area between us and the entrance gate.
Rumour is the music festival taking place in a week or so, just in front of the yard needs to install the toilet blocks pretty much to just a few metres from our stern. This meant there would be no room for a fire truck to pass to serve the boatyard's main building.
With this news, we stopped working immediately. We have plenty of experience with EVA (Emergency Vehicle Access) rules and design to know there is no chance we can stay in this place. The yard has not realised this huge problem they now have on their hands.
We called the other travel lift guy and started immediately discussing with them where will they place the hardstand posts in our next position so we could take advantage of this boat movement without costing us more work time and money.
We marked the areas they indicated and masked a generous area around them. We now have a new plan, we are going to apply the Coppercoat to these areas first!
We rushed washing thoroughly the areas defined by the masking tape and gave it a first round of cleaning with Isopropyl Alcohol before leaving for the day.
Day 17 (2022-06-18)
Probably one of our longest work days so far in the yard.
After yesterday's end-of-the-day news, we had to reshuffle our entire sequence of works to take the best advantage of the lemon of a situation we were presented with.
Early morning we cracked on with giving another clean with Isopropyl Alcohol on the areas defined the previous afternoon and prepared to apply the five coats of Coppercoat.
After applying the Coppercoat in the designated areas, we decided we could still advance with some of the work we had scheduled for today before the big news was given to us.
We decided to give two coats of barrier coat (Gelshield 200) and try to get back on track to the original sequence of works. The Gelshield was applied in alternating coats of green and grey making the hull look bizarre.
At this point, the yard manager is still clueless about what is going on and seems to think it won’t be necessary to relocate us. I informed him, in any case, we could only be moved in five days time because we have a special paint curing that cannot take the shock of the travel lift bands.
Day 18 (2022-06-19)
Another eight hours workday today, but this time always looking behind our shoulders at the very dark rain clouds forming. Two things in our mind, the first is the Coppercoat patches we already applied that cannot get wet yet, and the second is the Gelshiled we just applied that cannot get wet either!
Still managed to get two coats of barrier coat on the keel and bulb (it now has four coats of paint in total) and to start painting the raised waterline and the rudder (both with one coat).
We were extremely lucky the rain stayed a few streets north of the yard. Now that was a very close call.
Day 19 (2022-06-20)
A long day in the yard marked by the many pauses in between coats of paint.
Quite enjoyed seeing the boat painted in different colours. My favourite combination was green with grey.

We managed to get all the necessary coats of paint for the barrier coat, and now we will have a small pause on this project while we wait for all of it to cure for a couple of days before restarting again.
Day 20 (2022-06-22)
We started the morning by giving a light sanding over the areas we applied the new Gelshield barrier coat to ensure a good keying for the Coppercoat. We also keyed the Coppercoat patches.
The rest of the day was spent making sure the hull was super clear of any traces of old antifoul. Going up and down ladders moving them a million times, wiping the hull with Acetone, then washing it thoroughly (it has been four days since the patch Coppercoat application and water is no longer a problem)
Day 21 (2022-06-23)
Extremely slow day. We only worked on the Coppercoat project for two hours, but we had to wait all day until 5 pm till our allocated time slot, then we were relocated to the other side of the yard due to the music festival.
The travel lift guys are amazing and booked our movement for the end of the day so we could stay hanging on the slings for the night, allowing us to work on the base of the keel bulb.

With The Dream flying high in the sky (well as high as possible due to our rigging and hardtop), we finally got the opportunity to sand the remaining old antifoul paint and apply the primer and barrier coat on the very bottom of the keel bulb.
Day 22 (2022-06-24)
Half of the morning was spent getting The Dream sitting correctly on the hardstands.
When they removed the slings we realised they were very dirty and had left a grease stain on the hull that was already prepared for Coppercoat.
We spent the remaining of the day trying to remove those stains resorting to anything from Isopropyl Alcohol to dishwashing soap and Acetone. Most came out, but not all of it.
Day 23 (2022-06-25)
We had to resand the stained areas again. Wash, let dry and sand again.
A process that had to be repeated a few times consuming the entire day and our patience.
Day 24 (2022-07-01)
Finally, this morning we had the right weather conditions to apply the Coppercoat!
We divided the hull into areas of roughly 3.5sqm each (each kit covers 4sqm with five coats) to more easy to deal with the timing between coats and to ensure the correct amount of copper was applied. Cleaned the entire hull with Isopropyl Alcohol two times.
John embraced the task of applying the Coppercoat while I took on the task of preparing the kits and ensuring the copper stayed suspended in the epoxy during application.
After lunch, the wind picked up a bit making the process quite challenging and forcing us to stop for the day.
We applied five coats of Coppercoat on a bit more than half of the hull on the first day.
An exhausting nine hours non-stop workday.
Day 25 (2022-07-02)
A seven-hour workday to finish painting the hull of The Dream, this time we had no problems with the wind.
We are still missing the rudder and keel.

Day 26 (2022-07-03)
It took us five hours to prepare and paint the keel, rudder and final touches on the seacocks, but all five coats of Coppercoat are now applied throughout The Dream hull.
Day 27 (2022-08-15)
John spent the day giving a light sanding and abrasion to activate the Coppercoat as part of the preparations to return The Dream to the water.
Day 28 (2022-09-03)
After a big break of two weeks, The Dream finally got back on the slings to stay hung for the weekend (the slings got a new cover to avoid any stains) after one day delay due to the travel lift being under repair.
Finally, it was time to apply the Coppercoat to the last area, the base of the keel bulb!
Cleaned the area with Isopropyl Alcohol, we applied the five coats of Coppercoat and let it cure, in total we cured the Coppercoat for roughly 52h before returning The Dream to the sea.
Day 29 (2022-09-05)
Splash morning!
***The Dream is not affiliated or sponsored by Coppercoat or by Aquarius Marine Coatings Ltd, this blog post is based solely on our experiences with the product.
***You can find other posts of this series at Coppercoat antifoul treatment - considerations and costs (part 1)
***In the spirit of sharing our dreams and experiences we have shared this blog post in the NOFOREIGNLAND.COM website sailors community.
Comments