Transat - Repairs off the beaten track and another lesson learned - part 3
- Ana
- Apr 8, 2023
- 12 min read
Updated: Nov 18, 2023
With a plan already in motion in the form of a brand new autopilot coming our way and a new part to replace the broken one at a later stage ordered (giving us in the future two fully independent and operational autopilots), it was time to start preparing for the installation of the hydraulic pilot.
We wanted to install the new pilot the very next day after I arrived from Portugal with the unit, so there was a bit of work we could get ahead on.
The new unit would require a completely different setup.
We needed a custom-built mounting bracket for the hydraulic ram, a mounting bracket for the pump and a reinforcement plate for the quadrant (where the ram arm would connect). Through our contacts at a local Yacht Clube (that is what they call the marinas in Brazil) we got the contact for a local steel fabricator. The comments were a bit confusing ranging from "he takes ages" to "he is quite ok", but no one could show us some of his work, so we had to take a chance and have him fabricate some of the things we needed.
To avoid having the guy judge us by the size and looks of our boat and to try to ensure we got what we wanted and not what he might think we want, John built plywood models of the needed parts. Still, we were given the tourist price, or at least that is what we felt, but time was of the essence, and we couldn’t waste more time on it, hopefully, it would turn out ok.
It didn’t turn out as we expected. The parts looked just border limit ok as if done by an apprentice, not square or straight and despite the models fabricated by John, it was still required for us to make some adjustments (sending them back to the fabricator would be just another waste of our time and patience). We dry-fitted the backing plates for the quadrant reinforcement plate and confirmed they were not cut to the right shape. With a lot of patience, John managed to rectify these two stainless steel pieces using our tools.
It was now time for my flight to Portugal to get the new autopilot and the Victron BMS replacement that also broke on the crossing.
Yeah, did we forget to talk about what happened with the LiFePo4 system?
We did forget. The autopilot situation was so overwhelming that the BMS felt like peanuts.
We contacted our dealer complaining about the malfunction, and Diana from Victron Portugal was amazing, as always. She said it was no problem, we just needed to contact the local dealer for him to provide us with the replacement. It simply sounded too good to be true, and it was.
As soon as we contacted the Victron dealer for South America, they informed us they do not supply any Lithium related products, and therefore we would not find stock anywhere, and we would have to go through the import process, pay 100% duty and wait who knows how long.
Back to the discussion with Diana and the European sales manager, the word was: "Just get the part to them". Since I was going to fly to Portugal anyway, Diana expressed courier the replacement part to my mum's address immediately, so that item was already waiting to be picked up for a while.
This was an easy item to get through customs given the size and aspect. Just a simple little black box with some cable connection ports, it could easily be mistaken as an internet router.
It was a straightforward replacement if you don’t consider the circus positions required to rerun the data cables (while we waited to get the part we had to change the original system to run the inverter Multiplus rogue mode) back to the correct positions.
The big challenge was how to bring the new autopilot without getting caught by Customs entering Brazil, this thing was not only of considerable size but has these hydraulic pipes already correctly pressured and connected, limiting the options in terms of packaging.
I got rid of the box where it came in and the wood board where it was mounted. I prepared a small wooden piece to ensure the rod position was not going to change position during transport and to the best of my possibilities I packed it in one of our old suitcases, zip-tying it to the back frame of the bag (the structure that has the pull-out handle) to prevent it from moving around while being transported.
Between the suitcase and the new autopilot, I was already close to my weight allowance leaving only room for some clothes I could use to pad and protect the autopilot.
All I could do now was to hope to be lucky and not be stopped at Customs.
Funny enough I had been stopped by Customs on arrival to Lisbon for the first time in my life, my sailing duffle bag all cling-wrapped was considered suspicious, and the contents were also a bit strange. Simply shoes.
Upon arriving back in Salvador, the nervousness clicked in. The entire setting was conducive to it.
Only three queues for immigration (foreigners, Brazilians and priority), and only three counters. While in the queue a Polícia Federal officer asked to see tickets or boarding passes, which was quite strange considering there was only one international flight arrival. Upon my turn to the immigration counter the officer received a phone call from a colleague on domestic flights to check the identity of a passenger that is trying to board an internal flight using as ID a passport that although not new seemed to have never been used before, his name matched an arrest warrant. What an awkward situation to be in, waiting to get my passport checked while listening to all this. With the guy's identity confirmed (and presumably arrested at the domestic terminal) the officer stamped my passport without even mentioning the fact that I left the country just a week ago on a different passport (I took the chance to renew my passport while in Portugal) and that I only have 36 days left on my tourist visa waiver. I asked how many days can I stay, and he replied 90 days. Strange.
I proceed to the luggage pick-up room that is just around the corner. Bags are already circulating on the carrousel, and all the people that were ahead of me in the queues before are already gone. The luggage service seemed to be extremely fast here. As I walk closer to the carousel trying to see if my bag is already circulating I noticed two groups of suitcases already placed on the floor, close to ten pieces each, all different sizes, mine is among those. Bells start ringing in my ears.
Calmly I grab my bag giving it just a very quick look to see if it’s not damaged and proceed to the nothing to declare channel. As so many things are different in this airport the "nothing to declare" and "to declare" channels are at complete opposites ends of the room, while in most airports they are just side by side. There is no way one could say they got distracted and entered the wrong channel.
I turned to the narrow long corridor that has a Customs desk at its end with an officer sitting and several filming cameras behind him. As I approached he said something to me I don’t understand, my belly clinched while I apologise I didn’t hear him could he repeat?
He says: "Are you travelling together?”
I look back and see that the guy walking behind me is close to me. As I look forward again looking surprised I reply:” No, I don’t even know him", as I’m saying this I noticed that at least one of his suitcases was standing next to mine on the floor by the carrousel. Not only my ears are ringing, but my belly is also clenching, and my heart is now racing!
The officer says: "Mr X please stop here with your bags"
I’m surprised the officer addresses the man by his name he is on to something. I ask what about me can I proceed? He says yes, and I rush out of his front, turning left I find myself inside a duty-free shop. Great all I needed was a stupid labyrinth as I’m trying to get out of the airport as fast as possible!
As soon as I’m outside of the airport I finally take a proper breath of air, is stinking hot, and I’m wearing winter clothes. I wait for my driver and check the suitcase more carefully. All seems ok, with no signs of an oil leak (yes, there was also a 1 Litre bottle of hydraulic oil in the suitcase).
I arrive back at the boat, and John and I inspect the autopilot, it has not suffered any damage during transport, it is now 1 am Sunday and time to go to bed.
Sunday early morning we started the installation of the new autopilot.
The first step was to do a dry fit and assess exactly how much of the cabinetry we needed to cut to allow the hydraulic ram to be in a position as close as possible to correct. This is always a difficult moment, cutting holes in the boat or the finishes. With that done we repeated the process of dry fitting, ensuring everything countless times.
It was time to disassemble the steering cables system and remove the quadrant, but first, we made notes regarding the tension of the cables and where each cable goes just in case we have a memory challenge.
We installed the emergency tiller to ensure in any eventuality we could still steer (we were in a mooring ball).
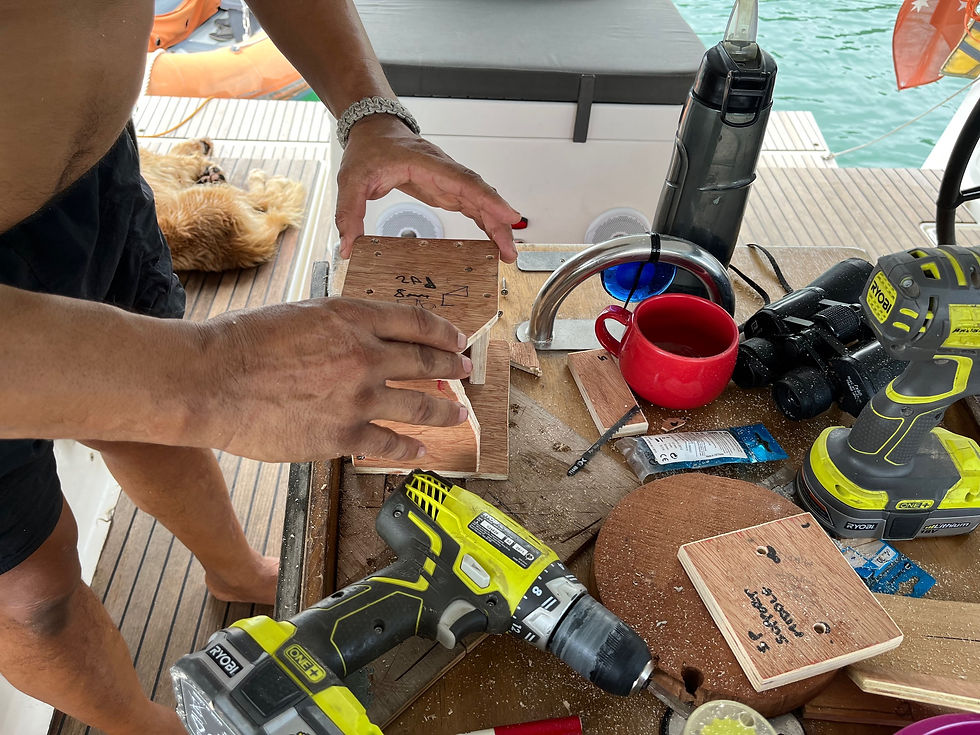
With the quadrant now on the cockpit table we secured the new backing plates in position with clamps and positioned the reinforcement plate to mark the holes we will need to drill both on the quadrant and the backing plates. We also marked the position of the rudder feedback unit and the pin where the hydraulic ram arm will connect.
We felt pretty satisfied with our progress so far.
With all the necessary holes drilled at the expense of quite a few drill bits, we returned the quadrant to its position temporarily to do another dry fit, now with the new pieces already in their position. We established the new position for the rudder feedback unit, and that’s when we noticed that the unit had not been correctly installed by the commissioning team way back in 2013 before The Dream was The Dream. Annoyed with our findings we realised that this is the reason why our helm has never been aligned, and that needs to be corrected. We spent the remaining of the day working on rectifying that.
Early afternoon we decided to conclude our work day, go for showers and lunch at the club and catch up with our French neighbour, it has been pouring with rain most of the day (apparently the week I was in Portugal coincided with the beginning of the rainy season) and the day looks pretty miserable despite the high temperatures.
Our neighbour was working hard on his steel boat trying to tackle the rust areas, and the weather was not helping him at all. As we chat away I thank him for the nifty trick with the lemon for the drill bits. He looks at me as if saying what the heck are you talking about and simply says: "Onion!", in such a blunt French way that makes me crack up laughing.
While I was away, he and John talked a lot about steel works, and he had mentioned this cool trick to assist with drilling holes using an onion as a lubricant, and somehow what John memorised was that lemon was the secret. We had just drilled several extremely difficult holes using a lemon as a lubricant and had thought it had worked better than without it!
The following morning we repeated the process of confirming the position of all items and confirmed that the quadrant reinforcement plate needed to be slightly cut in a corner to avoid fouling the hydraulic ram, not an easy feat given the thickness of the plate but with persistence John gets it done.
With that done we proceeded on installing the backing plates and quadrant reinforcement plate permanently, applying a generous layer of Sicaflex between the different metal parts (the quadrant is made of aluminium, and the new pieces are made of stainless steel) before bolting them together.
Achieving this took us our entire work day.
We returned the quadrant to its position and reassembled the cable system. Now we could move although still without the autopilot.
The next morning we needed to go back to the airport to visit the Polícia Federal to get our visa extensions done. This was going to occupy most of our morning so we decided that in the afternoon we would leave the Yacht Club and go on to another mooring ball but in a nicer place.
The third day of our installation was already on Wednesday when we tackled the rest of this project.
The next step was to install the mounting bracket for the hydraulic ram unit and mount the unit on it. This time we used an onion, and it worked even better than with a lemon.

We mounted the bracket on the structural bulkhead and the unit on the bracket, we could now assess where could we mount the pump following its requirements. After a few trials with the hydraulic pipes and the curves, they allow we decided on the bracket we still need to build for the pump but decided that with our experiences with the local steel fabricator, it would be best we build a temporary piece in marine ply and get the part done at a later stage.

The last item to decide in terms of positioning was the oil reservoir, but we had planned to have this mounted on the cockpit lazerette in front of the main helm station, as it would be a convenient location for refills and service. For that, we needed to disconnect the reservoir from the hydraulic pipe carefully, pass the pipe through the steering system slot and ensure its correct position before reconnecting it to the reservoir and then fixing the reservoir to the lazerette. We could now finally fill the reservoir, open the valve and then connect the hydraulic ram arm to the quadrant for the first time.
We tested the steering by hand, turning it full lock in both directions while checking to confirm nothing was getting fouled. The steering felt so smooth compared to when the old unit was installed.
We decided to give a quick test of the autopilot despite being on a mooring ball. We turned it on and after a few quick tests of turning it to starboard and port, we realised the pilot was steering backwards. When we pressed starboard it was turning port, and when we pressed port it was turning starboard. Panic!
We had already been on an emotional rollercoaster with this project always striking extra challenges, nothing was running smoothly we felt.
Nothing on the manual gave instructions on the set-up, so we checked the internet again and found in a few forums regarding older models the mention of reverse polarity, switching cables to achieve it and that sounded a bit risky to do on a brand new unit were we had no technical support. John started navigating the menus on the pilot control display and eventually found something that could relate to the reverse polarity mentioned on the forums. He found a screen regarding motor phasing (phase A and phase B), he decided to give it a go and just like that the autopilot was now running in the right direction as prompted.
With all this rush of emotions, we decided to stop for the day and go enjoy the shallows by the mangroves together with some local sailors we had met.
We needed to wait for Slack Tide to go do the calibration etc.
One day later, after having fun with our new friends we cut loose from the mooring ball at slack tide and started the autopilot calibration. I can only imagine what they thought seeing us doing random circles and zigzags, all seem to be going ok until we got to one of the last screens where we needed to align the GPS with the magnetic compass. The trouble now is that our magnetic compass is calibrated to have the old autopilot unit on underneath so now we are not sure of how accurate it is, the other helm station was also quite different, a hand-bearing compass was proving difficult, and the phone was also giving us different values. We started to suspect that the Baía de Todos os Santos was some sort of deviation but since we don’t have paper charts we could only guess so we de idea to leave it as is and redo the calibration later.
Then one of us went inside to see the pilot unit working, and that was when we discovered, to our surprise, that the new mounting bracket 6mm thick was flexing. Panic, again.
We returned to the mooring ball, talked to the French neighbour that had found another steel fabricator, and the following day we headed back to Salvador to take the mounting bracket to this new guy for reinforcement. What a bummer having to disassemble the autopilot, but this needed to be addressed urgently.
The new fabricator gave us of course the Gringo price but at least fixed the part in 24h. Still not a pretty job, but well welded. We reinstalled everything again and went out to test it.

There was still some movement on it, but now very limited, we decided we could proceed like this and try to find another steel fabricator to do more work on this piece later.
It seemed now we had at least a working pilot we just needed to gain confidence in it.
***In the spirit of sharing our dreams and experiences we have shared this blog post in the NOFOREIGNLAND.COM website sailors community.
Comments